|

pliance Hardware
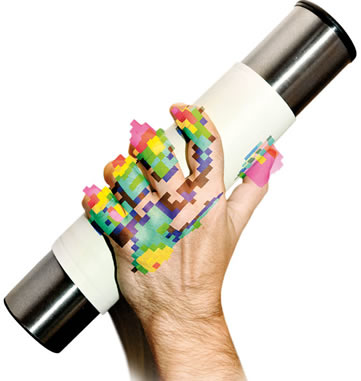
pliance systems offer state of the art technology for pressure distribution measurement between soft and curved surfaces.
As in all physical measuring systems, the most important component is the sensor technology. pliance works with capacitive transducers in a matrix configuration. The elasticity of the sensor mats permits conformability to 3-dimensional deformations.
The pressure transducer elements contain high-tech elastomers manufactured by novel. The restoring force, range of force, threshold, hysteresis, temperature effect, frequency response and other characteristics are determined during the manufacturing process. This makes it possible to adapt the sensor characteristic to different measuring needs. The elastic measuring mats are available in various sizes, sensor configurations and pressure ranges.
novel developed an analyzer technology that not only allows individual calibration curves for each sensor, but also individual dynamic amplification control and crosstalk suppression, resulting in very accurate and reproducible pressure values. The pliance analysis can work with a PC via the USB interface. Notebook computers or even a pocket PC can be used for mobile tests.
The pliance analyzers vary from small portable 16x16 channel units to large 112x112 channel units with a wide range of options, such as master-slave synchronization of several systems, dynamic amplification control, synchronization of video systems and analog inputs for accelerometers.
Technical data for pliance-x and pliance-x 32 system
dimensions (mm) |
150x100x40 |
weight (g) |
400 |
number of sensors (max) |
256 (pliance x-32 1024) |
measurement frequency |
20,000 sensors /second |
storage type |
32MB internal flash |
computer interface |
fiber optic/USB and Bluetooth TM |
operating system |
Windows 7, 8.1, 10 |
sync option |
fiber optic/TTL, in and out |
power supply |
NiMH battery |
loadpad
The loadpad measures the normal total force using a thin, flexible sensor. Based on a new patent, it is the first sensor which can accurately assess the total force even if heterogeneously loaded across the sensor surface. The loadpad sensor has matchbox-sized electronics and communicates wirelessly via Bluetooth with a smartphone. The force values are displayed on the smartphone in real time. The user can also receive immediate feedback regarding the applied force via an auditory, visual, or vibratory signal. The measured data can be stored on the smartphone and to the cloud and additionally transferred to a computer for a more detailed analysis. Long-term measurements allow the evaluation of different parameters such as impulse, load frequency or loading rate.
The loadpad app can be modified for specific applications. It is easy to use, offers numerous display options and allows the analysis of various parameters. Data can also be exported to an ASCII file for additional assessment not included within the app. Additionally, the Windows loadpad analysis software offers an extensive evaluation of the loadpad data on the computer.
The loadpad sensors are available in several standard sizes and with different sensitivity and maximum loads. In order to achieve an optimal adaptation to the intended measuring surface, the loadpad sensor can be produced with different material coverings. The sensor can also be manufactured with a maximum of three sub-areas if it is necessary to distinguish different loads across the sensor surface. The loadpad sensors can be configured accordingly to customer-specific requirements in terms of shape, size, sensitivity, and surface coatings. The loadpad accurately measures a complete assessment of the total force in the normal direction to the sensor.
loadpad AD sensor placed on a crutch
. Click here to learn more.
MT loadpad app display. Click here to learn more.
manugraphy - hand diagnostics
The manugraphy system is an accurate and reliable system designed to measure hand forces while gripping. Until now, functional hand diagnostics only quantify the total force while gripping, such as with a dynamometer. However the manugraphy system, developed by novel, offers a key advantage over the conventional systems: it is able to determine the force of each individual finger as well as the phalanges. The individual force contributed by each part of the hand – the finger, phalanx, or palm – is measured separately.
With this type of a detailed and objective analysis of the different hand locations, the user is able to compare the patient’s hand function in situations such as before and after a surgery. Additionally, the patient’s progress in rehabilitation can be better evaluated. The manugraphy system can also provide audio feedback which can be used in physical therapy. The patient can carry out different gripping exercises independently, and therapy results can be analyzed objectively. Standardized or customized reports can be created.
Click here to learn more.
Synchronization hardware
Both wired and wireless synchronization is available for the pliance system. The wireless synchronization device allows untethered synchronization with other measurement systems such as motion capture, EMG, video, etc.
Click here to learn more.

| |

Download Brochures
pliance sensors (2.11 mb)
pliance manugraphy (3.66 mb)
pliance prothesis (3.5 mb)
pliance saddle (245 kb)
pliance wheelchair (2 mb)
pliance tire (800 KB)
pliance FTM (692 KB)
loadpad (1.2 MB)
loadpad horse (280 kb)
texsens (129 kb)
MT loadpad (1.1 MB)
Get Acrobat Reader
Download DivX video codec to view our videos
|